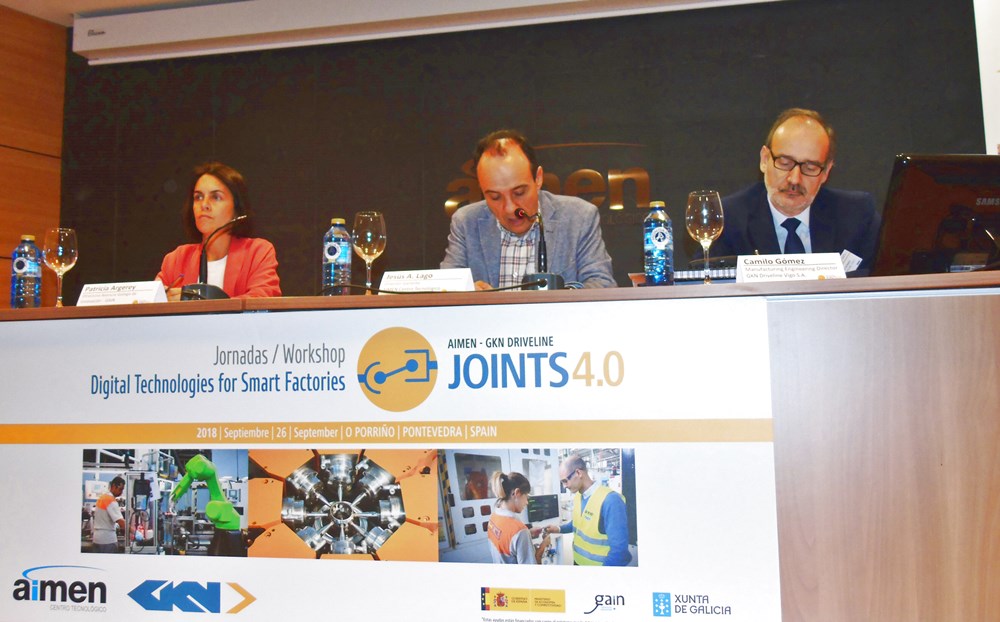
Una jornada a la que han asistido más de 70 representantes de la industria gallega y en cuya sesión han participado un total de doce ponentes pertenecientes a empresas y universidades tanto españolas como de Alemania, Reino Unido o Grecia, que han presentado y analizado diferentes tecnologías y aplicaciones orientadas a la fábrica del futuro
El Centro de Aplicaciones Láser de AIMEN acogió ayer la jornada “Digital Technologies for Smart Factories”, organizada en colaboración con GKN Driveline Vigo, en el marco de la Unidad Mixta de Investigación JOINTS 4.0. A esta sesión, orientada a presentar soluciones tecnológicas dirigidas a implantar la fábrica inteligente en la industria, han asistido más de 70 representantes del sector de automoción, industria auxiliar y metalmecánico.
La jornada ha sido inaugurada por la directora de la Axencia Galega de Innovación, Patricia Argerey; el director gerente de AIMEN Centro Tecnológico, Jesús Lago; y el director de ingeniería de fabricación de GKN Driveline Vigo S.A., Camilo Gómez.
En su intervención, Patricia Argerey se ha mostrado muy satisfecha de los trabajos realizados hasta ahora por la UMI JOINTS 4.0, que tuvo la ocasión de visitar hace poco más de un año y que ahora generan este espacio de encuentro para compartir conocimiento con el resto de la industria. Además, ha manifestado que “las unidades mixtas generan soluciones, resultados concretos, que permiten innovar a todo el tejido empresarial ganando competitividad.
Por su parte, Jesús Lago ha destacado que “la colaboración directa entre AIMEN y GKN Driveline Vigo en JOINTS 4.0 es un claro ejemplo de cómo la innovación abierta consigue excelentes resultados para avanzar en la implantación en Galicia de la Industria 4.0, un camino en el que los centros tecnológicos como AIMEN se convierten en aliados imprescindibles de las empresas, posicionándose como proveedores de servicios de alto valor añadido”.
Asimismo, Camilo Gómez ha destacado la importancia de colaboraciones como las que se establecen en las unidades mixtas de investigación, ya que implica un acercamiento necesario entre el mundo académico e investigador y la empresa.
La jornada ha estado orientada a dar a conocer tecnologías y aplicaciones orientadas a la fábrica del futuro, soluciones necesarias para alcanzar el objetivo principal de la Unidad Mixta de Investigación JOINTS 4.0: ayudar a convertir a la planta de Vigo del Grupo GKN en la mejor fábrica del mundo en la producción de juntas homocinéticas y elementos de transmisión mediante su transformación en una fábrica inteligente referente de la industria 4.0.
En la sesión han participado un total de doce ponentes pertenecientes a empresas y universidades tanto españolas como de Alemania, Reino Unido o Grecia, que han presentado y analizado diferentes tecnologías y aplicaciones orientadas a la fábrica del futuro.
En el marco de la jornada, GKN Driveline Vigo ha mostrado su visión del concepto ‘Smart factory’ y ha enumerado los pasos para convertirse en una fábrica inteligente. Por su parte, AIMEN ha presentado resultados concretos de la investigación desarrollado en el marco de la Unidad Mixta de Investigación enfocados a la utilización de técnicas de ‘Deep learning’ para la detección de defectos en piezas.
Otras de las temáticas tratadas durante la jornada han sido las plataformas de datos para la gestión en la Industria 4.0, herramientas de simulación de alta precisión para procesos de fabricación basados en láser, sistemas para la colaboración humano-robot en operaciones de ensamblaje, sistemas para la sensorización y monitorización de procesos, tecnologías de fabricación aditiva, etc.
Algunos de los retos tecnológicos de la UMI JOINTS 4.0, que cuenta con un presupuesto de 4.798.474 € (incluye las fases de creación y de consolidación) y prevé crear un total de siete nuevos empleos; son generar y aplicar nuevas tecnologías y conocimiento para la fabricación inteligente y sostenible, creando una base tecnológica sólida que permita producir lotes cortos y flexibilizar los procesos de fabricación, eliminando los conceptos de ineficiencia y defectos (tendiendo al “zero defects manufacturing”).
Asimismo, pretende desarrollar y poner en práctica tecnologías de mantenimiento inteligente en equipos de mecanizado; reconfiguraciones de equipos para adaptarlos a las nuevas necesidades de fabricación; sistemas de monitorización y control de procesos de producción incluyendo la generación temprana de alertas, o equipos prototipo ad-hoc para el control de calidad de piezas en línea.